About Us
60 years, 3 generations and
100% Indigenous
DCL Engineering Group 60 years, 3 generations & 100% Indigenous. DCL has been servicing industry in mechanical breakdown repairs and engineering for 60 years. The company has three branches, located in Wollongong, Fairfield and Newcastle with a team of experienced professionals using state-of-the-art equipment and technologies.
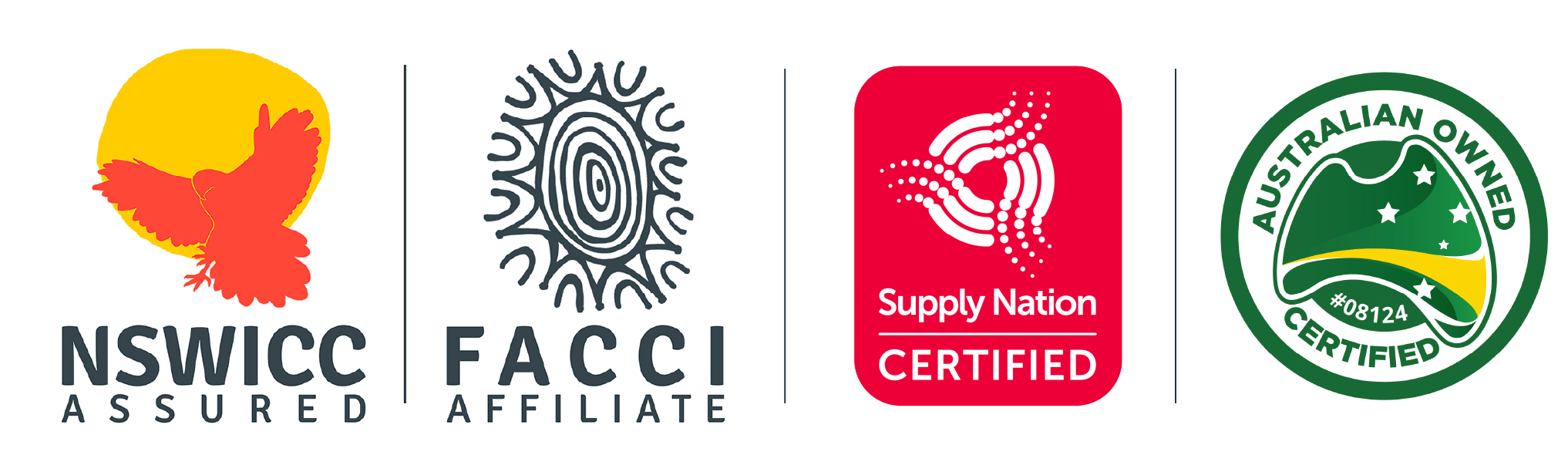
60 years | 3 generations | 100% Indigenous company
ENGINEERING (MACHINING & FABRICATION)
A core focus of DCL is the engineering division using modern technologies, creating solutions to minimise machinery wear and complete machinery overhaul & repairs. Offering an end-to-end solution for clients with reverse Engineering using 3D Cad design, Engineering- FEA, CNC machining, fabrication & specialised welding services. Providing clients with start to finish in-house complete solutions, there is no need to visit multiple workshops to have your job completed. The job will be completed more efficiently and allows the client to have better cost control. To further enhance the capabilities to meet their customer needs in heavy machining, DCL have invested in very large CNC machinery to further increase accuracy and efficiency.
GEARBOX / TRANSMISSION OVERHAUL
Over time DCL has become one of the most respected overhaul workshops on the Eastern seaboard. Specialising in repair, refurbishment and the service of industrial gearboxes of all brands and models, including fluid couplings, drive shafts and braking systems. Using the latest technologies and equipment combined with load testing facilities in Sydney and Port Kembla workshops.
LIFT INDUSTRIES
A mechanical parts manufacturer & repairer since 1960 as well as the major supplier of traction and diverter sheaves to the lift industry in Australia and New Zealand, DCL can offer mechanical services and equipment to the lift industry.
Services Include:
- Australian Supplier of Work Cover Approved – CWT Props
- Supplier of Rope Sheave Gauges
- Lift Mechanical Repairs and Gearbox Transmission Consultancy
- Onsite Machining of Sheaves
- Design – FEA & Manufacture of all brand Elevator Traction and Diverter Sheaves
- TRACTkote® Coating System for Traction and Diverter Sheaves
- Gearbox Repair
AIMS
DCL Engineering Group’s Asset Integrity and Maintenance Support division provides several technology-based services to improve your maintenance practices and equips you with the tools to make informed maintenance decisions. These services include: Condition Monitoring, Laser Alignment, and CMM/laser Tracker inspection services to its customers. We have extensive CM experience with a wide variety of equipment.
SURFACE ENGINEERING
DCL Surface Engineering division a skilled team of engineers with combined 90 years’ experience in surface engineering technologies, it caters for the growing need of industry requiring surface engineering solutions using the latest thermal spray processes to enhance surfaces, to repair worn components back to their original surface or using them in innovation for enhancements and cost saving solutions in all industries using Arc Spray, High Velocity Oxygen Fuel (HVOF), Plasma Transferred Arc (PTA) and Powder Sprays. Offering our services for a variety of industries and equipment, including industrial, earthmoving, electric motors, pumps, transmission parts.
Proud NSW Indigenous Chamber of Commerce member.
At DCL we practice the company mantra – IMAGINE – BELIEVE – CREATE – ACHIEVE in all elements of the business. Think extreme precision, think extraordinary challenges, think incredible latest AI technologies that requires specialised techniques, think analytical, think striving to pioneer.
If you can Imagine it – DCL can do it.
Gearbox Industries
With knowledge and know-how from decades of experience coupled with state-of-the-art equipment DCL is equipped to overhaul or replace industrial gearboxes for varying industries, offering high-quality and cost-effective solutions.
- Mining
- Pulp and Paper
- Marine & Port Crane Operations
- Cement
- Food & Beverage
- Steel
- Rail
- Amusement
- Oil & Gas
- Lift
- Sugar
- Power
- Rubber & Plastics
- Defence
- Water & Waste Water
DCL Engineering Acknowleges the Traditional People of the Lands we work from and visit, we recognise their continuing connection to the land and water, to the dreaming and to all living things.
We pay our respects to ancestors, and the elders, past, present, and future, whose strength and guidance continually nurture us.
We pay tribute to Aboriginal and Torres Strait Islander leadership within our communities, within business, and amongst our youth.